Scheduling for Preventive Maintenance: Proactive Strategies
Preventive maintenance remains a cornerstone of efficient operations. Especially in the field of management where equipment and assets are dispersed across various locations. By adopting...
Sep 03, 2024
# of Minutes to Read
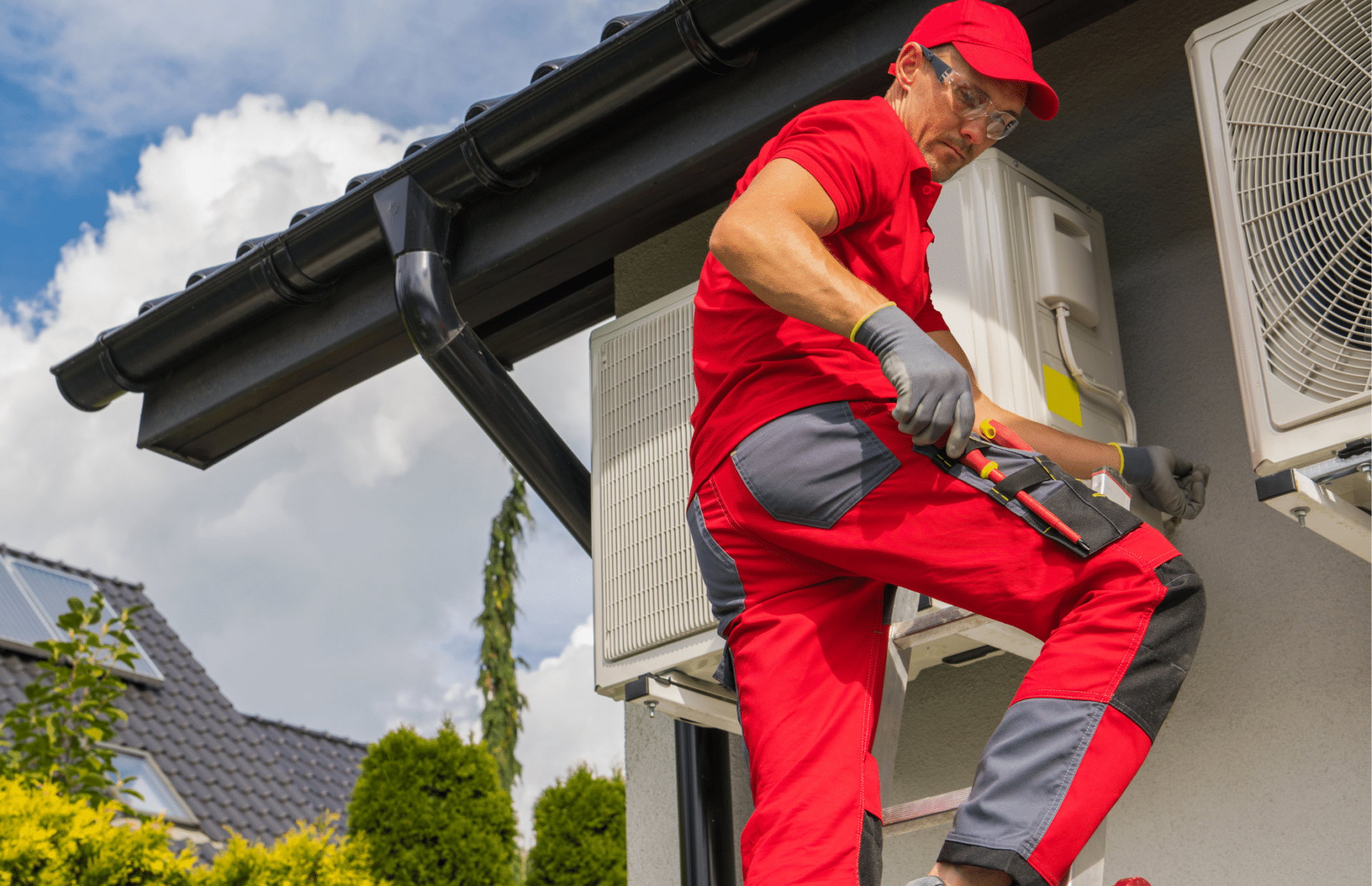
Preventive maintenance remains a cornerstone of efficient operations. Especially in the field of management where equipment and assets are dispersed across various locations. By adopting proactive strategies for scheduling preventive maintenance, organizations can ensure optimal functionality of their assets, minimize downtime, and enhance service delivery. This blog delves into effective preventive maintenance practices tailored specifically for field management.
What is Preventive Maintenance in Field Management?
Preventive maintenance in field management involves a proactive approach to the care of equipment and facilities dispersed across various field locations. This strategy includes regular and systematic inspection, cleaning, lubrication, adjustments, and repairs to ensure that all assets are operating at their best. The primary objective is to identify and address potential issues before they escalate into significant problems that could disrupt operations. By adhering to a scheduled maintenance routine, organizations can prevent unexpected equipment failures, minimize downtime, and enhance the overall efficiency and reliability of their operations. Additionally, preventive maintenance helps extend the lifespan of assets, ensuring a better return on investment and maintaining high standards of safety and compliance with industry regulations.
Benefits of Proactive Preventive Maintenance
The proactive scheduling of preventive maintenance brings several advantages:
- Minimized Equipment Failures: Regular maintenance reduces the frequency of equipment failures in the field, ensuring continuous operations.
- Improved Resource Allocation: With scheduled maintenance, organizations can better allocate resources, including personnel and budget, avoiding the higher costs associated with emergency repairs.
- Enhanced Customer Satisfaction: Reliable equipment performance means better service delivery, which in turn increases customer satisfaction and trust.
- Increased Safety: Preventive maintenance also involves safety checks, which protect not only the equipment but also the field technicians who operate them.
- Compliance and Standards: Regular maintenance ensures compliance with industry standards and regulatory requirements, which can vary significantly across different regions.
- Cost Efficiency: Although preventive maintenance requires upfront costs, it is far less expensive than emergency repairs and replacements.
- Increased Safety: Regular maintenance ensures that all equipment operates safely, reducing the risk of accidents.
- Enhanced Equipment Efficiency: Well-maintained machines operate more efficiently, using less energy and reducing operational costs.
- Longevity of Assets: Regular upkeep extends the life of machinery, ensuring that investments last as long as possible.
Strategic Planning for Preventive Maintenance in Field Management
- Asset Inventory and Prioritization: Create a comprehensive inventory of all field assets and prioritize them based on their criticality to business operations. High-priority assets should have more frequent maintenance schedules.
- Leverage Technology: Utilize field service management software like RazorSync that supports GPS tracking and mobile communication. Such tools can schedule preventive maintenance tasks based on real-time data and provide technicians with access to maintenance histories and checklists while on-site.
- Standardize Maintenance Procedures: Develop standard operating procedures for maintenance tasks. Standardization ensures that maintenance is performed consistently, regardless of which technicians are deployed.
- Training and Certification: Regularly train field technicians not just on the technical skills required for maintenance but also on the latest industry practices and safety protocols.
- Remote Monitoring and IoT: Implement IoT sensors to remotely monitor the conditions of field equipment. Sensors can provide real-time data on equipment performance, enabling proactive maintenance decisions before manual inspections identify potential issues.
- Feedback Loop: Establish a feedback mechanism where field technicians can report potential issues or suggest improvements. This input is invaluable for refining maintenance schedules and procedures.
- Risk Assessment and Prioritization: Begin by assessing the risk associated with each piece of equipment failing. Those with higher risks of causing significant operational or safety impacts should be prioritized for preventive maintenance.
- Develop a Maintenance Calendar: Create a detailed schedule that outlines when each piece of equipment will undergo maintenance. This calendar should consider the manufacturer’s recommendations, past maintenance records, and the operational schedule of the equipment.
- Utilize Maintenance Software: Leveraging field service management software, such as RazorSync, can automate scheduling and record-keeping. It can provide reminders for upcoming maintenance events and track the history of each piece of equipment.
- Train Your Team: Ensure that all maintenance staff are trained not only in performing the maintenance but also in recognizing signs of potential equipment failures. Knowledgeable staff can identify issues before they escalate.
- Review and Adjust the Schedule Regularly: The effectiveness of preventive maintenance schedules should be reviewed periodically. This review will help in adjusting the schedule based on new insights, changes in equipment usage, or updated manufacturer recommendations.
- Plan for Spare Parts Management: Ensure that critical spare parts are available when needed. This reduces the time spent waiting for parts to arrive, speeding up the maintenance process.
The adage “prevention is better than cure” aptly applies to maintenance management. A well-planned preventive maintenance schedule is an indispensable strategy for any organization that relies on machinery and equipment. By being proactive, companies can significantly reduce the likelihood of equipment failure, ensuring smooth and continuous operations. Remember, the goal of preventive maintenance isn’t just to maintain but to optimize and ensure reliability for all your operational needs.
Incorporate these strategies into your maintenance planning to enhance the effectiveness and reliability of your equipment, ultimately contributing to your organization’s overall efficiency and productivity. Ready to streamline your maintenance processes and boost your productivity? Try RazorSync for free today and see how our powerful field service management software can transform your business. Start Your Free Trial Now!